Turbomix-60 | TEKNİK DETAYLAR | Turbomix-60 | TEKNİK DETAYLAR |
---|---|---|---|
PRODUCTION CAPACITY | 150-200 HOUR | TOTAL MOTOR POWER | 220 kW |
MAX. FEEDING | 600 MM | GENERATOR - OPTIONAL | 380 kvA |
ROTOR - INLET SIZE | Ø1200X1000MM |
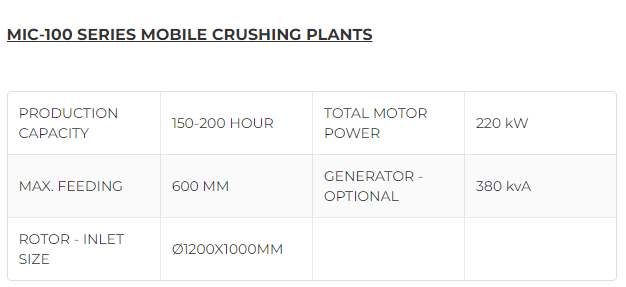
MIC-100 Mobile Primary Crushing Plant
MIC-100 Mobile Primary Crushing Plant is produced on a single chassis as rock feeding bunker, impact crusher and stock belt.
MIC-100 Mobile Primary Crushing Plant which can be easily transported on a single chassis with a hammer, easily crushes soft stones such as limestone, gypsum and marble then sends it to the stock area.
MIC-100 Mobile Primary Crushing Plant long years of service life for our customers with proven durability. It has been specially designed by our engineers to provide
The MIC-100 Mobile Primary Crushing Plant is the number one solution for stone crushing, providing minimum footprint and maximum performance in the field thanks to its normally minimized crusher size.
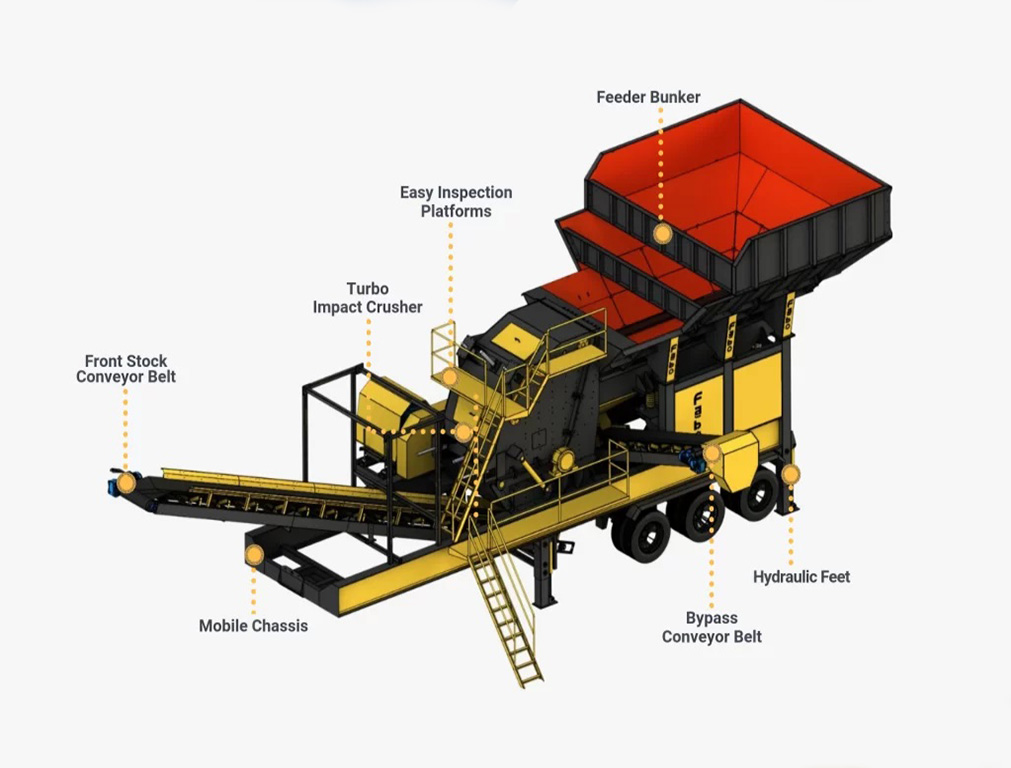
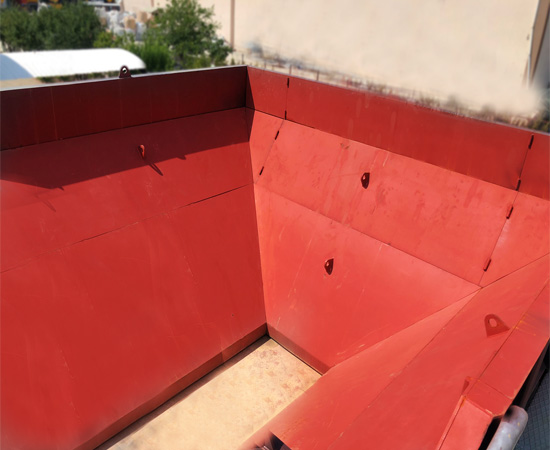
Vibrating Feeder Bunker
FABO Vibrating Feeder Bunkers have been developed by our engineers in a user-oriented manner so that the crusher on which it is positioned can operate with high efficiency.
The working intensity of the feeding bunker and primary impact crusher is coupled with the automation system.
This feature works in two steps.
1st step: If the density of the crushed product in the crusher is high, the amperage of the crusher increases, this rise is detected by the automation system and the vibration of the bunker decreases, preventing the product from accumulating in the crusher feeding chute. This feature prevents wear of the crusher.
Step 2: If the density of the crushed product in the crusher is low, the amperage of the crusher decreases. This decrease is detected by the automation system and bunker vibration increases. The feeding bunker starts to deliver the products to the primary impact crusher faster. This feature keeps the production capacity at the maximum level.
A1 quality springs, which provide the vibration of the bunker, have been specially designed and their working capacity has been maximized.
Our product, which has a 25 m3 rock feeding feature, is one of the special work machines that our company put forward with its quality and experience. Our product, which is durable and ideal for long-term use, is produced in accordance with CE standards and does not contain any substances that may endanger human health.
Primary Impact Crusher
FABO primary impact crushers are designed to crush soft and medium hard stones with high rotor speed. It is considered as the heart of the mobile system it is on. It ensures that all parts on the chassis work in harmony with each other, FABO quality, and wide warranty coverage, provides confidence and customer satisfaction with its 24/7 accessible support line.
With the help of high-speed rotating rotor breaking bars, the products poured from the feeder are crushed with the help of pallets. Hydraulically adjustable rods allow the products to be obtained in the desired size.
Liners and pallets prevent wear of the FABO primary impact crusher and offer a long service life. Protective linings can be easily replaced. And the service life can be increased by changing the direction of the pallets.
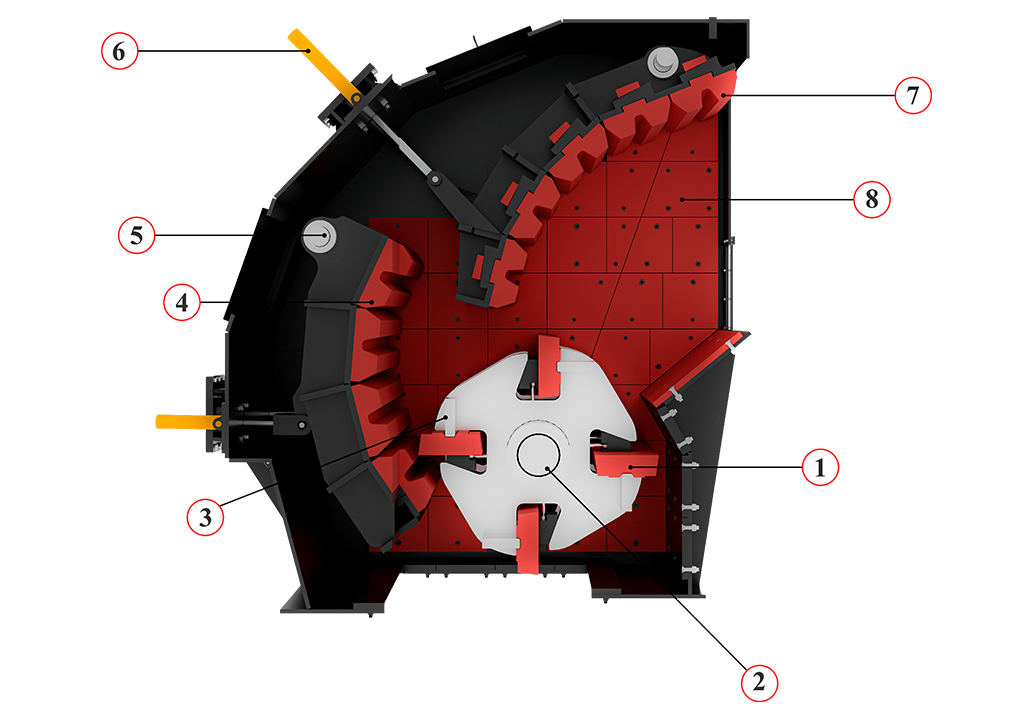
Interior view of the Primary Impact Crusher
Turbomix-60 |
---|
1- Crusher Pallets |
2- Crusher Rotor |
3- Pallet Holder Lock |
4- Crusher Lower Pendulum |
5- Pendulum Shaft |
6- Pendulum Adjustment Mechanism |
7-Crusher Upper Pendulum |
8-Side Linings |
Stock and Return Bands
With its foldable structure, it minimizes the dimensions of the machine it is on. Optionally, the number and length of tapes can be increased upon the request of the user.
10 mm EP 125 4-ply Band elastics, moving on 4mm st 37 Twisted Sheet, perfectly transport the aggregate coming out of the sieve to the area desired by the user in the most efficient way. The band tires, which are produced resistant to wear, will never let you down and offer a long service life.
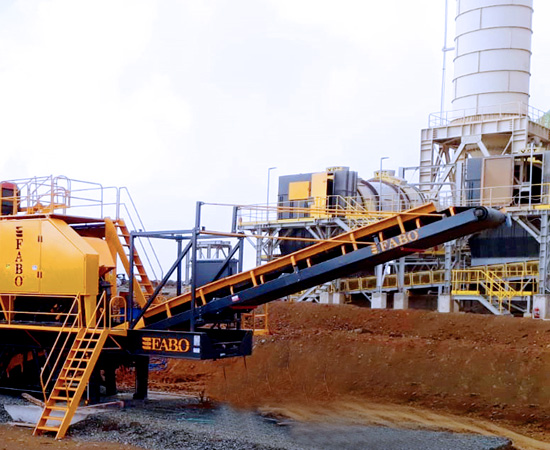
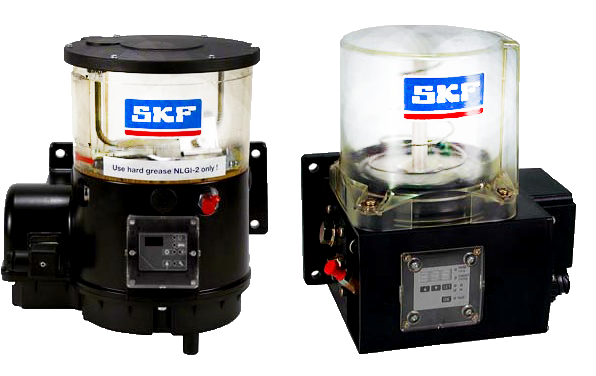
Automatic Lubrication System (Optional)
The Automatic Lubrication System is the system in charge of sending the grease that is reduced during the use of the crushing plant and needs maintenance to the relevant part.
It distributes the grease evenly to all components of the mobile crusher that needs lubrication and provides perfect lubrication.
The automatic lubrication system, which provides great ease of maintenance, finishes the lubrication process in seconds without the need for manpower. It allows to use the Mobile Crusher Plant in the most efficient way.
It uses the amount of oil in the most ideal way during lubrication and minimizes the maintenance cost of the user.
Hydraulic System (Optional)
Hydraulics is the system that enables the parts on the crushing plants to move easily. Opening, closing and moving the machine’s carrying legs, feeding bands, bunker covers and crusher feeder can be given as examples.
Hydraulic System Working Principle:
With the movement of the control arms, the hydraulic oil in can activate and the material to which the hydraulic system is connected the desired direction.
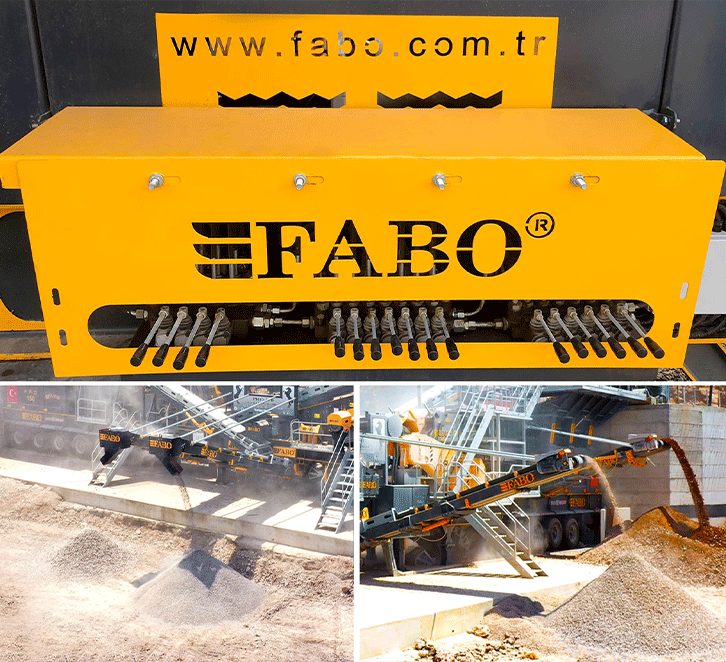
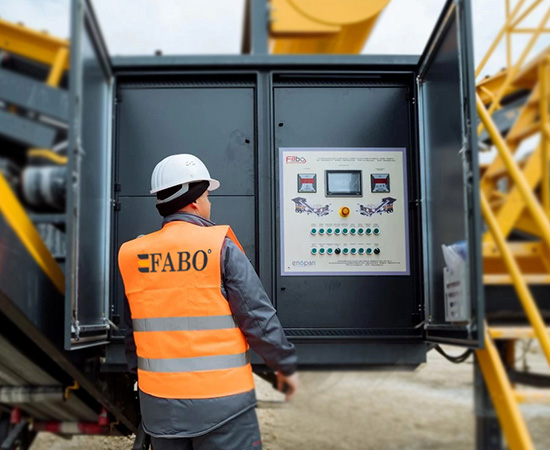
Automation System
MIC-100 Mobile Primary Crushing Plant is controlled by a full automation system. Thanks to the automation system panel on the machine, the working mode of the machine is adjusted. The working principle of the machine can be easily adjusted according to the shape of the material loaded by the user into the vibrating hopper. Many features such as Crusher Rotor Speed, (Optional) Bunker Vibration Speed, can be adjusted with the automation system.
The automation system, created by Fabo engineers, has been put at the disposal of its users in its most up-to-date form, taking into account all the tests performed from production to delivery.
It offers the opportunity to control the machine from anywhere in the world by using the remote connection feature with internet connection.
The automation system that allows you to use the Mobile Crushing Plant in the most efficient way has been prepared with PLC and serves its users with the most advanced state of technology.
Brake Axle System
The main factor that enables the MIC-100 Mobile Primary Crushing Plant to be moved easily is the axles at the rear. The load distribution of the crusher is calculated by our engineers and the number of axles and their position are determined.
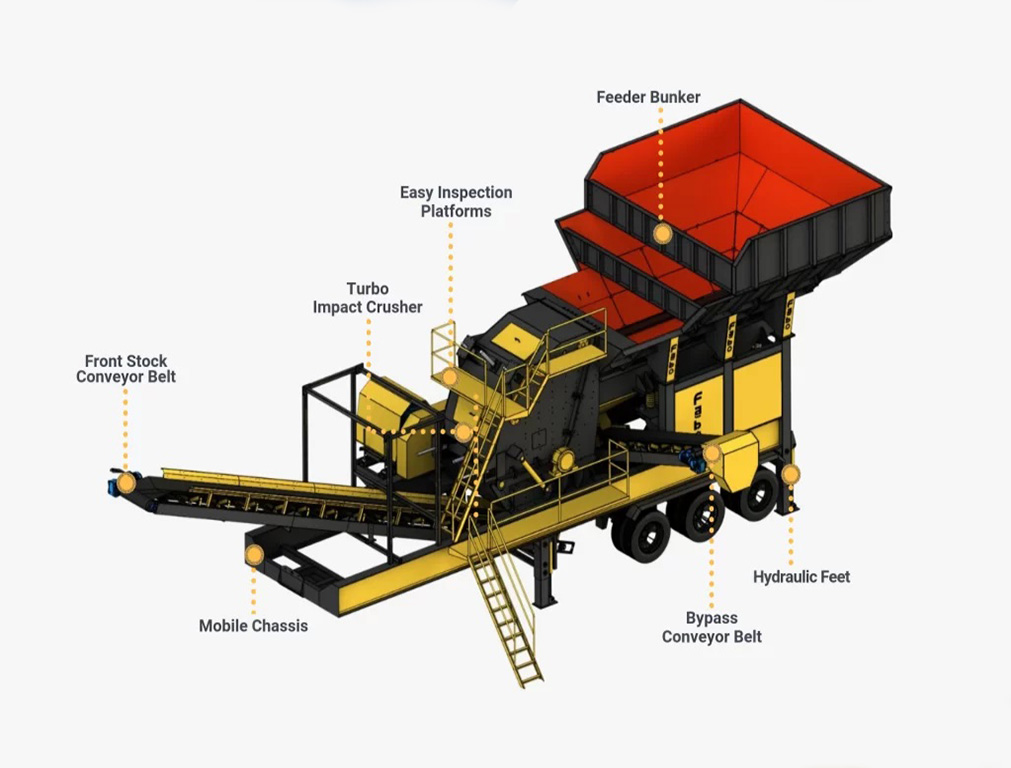
Shipping
Fabo MIC-100 Mobile Primary Crushing Plant minimizes the time and cash loss of the user with its ease of transportation. The MIC-100 Mobile Primary Crushing Plant developed by our engineers can be easily moved on a single chassis with a truck. Fabo MIC-100 Mobile Primary Crushing Plant , which is moved on axles, is ready for transportation in 10 minutes.
The MIC-100 Mobile Primary Crushing Plant, which we have created as a result of 18 years of knowledge and work, has been designed in the most ideal way for the user with its crushing capacity and easy transportation.
The brake system in the axle system has increased the life and property safety of the user to the highest level and has written its name in the sector with gold letters with 0% accident rate.
Fabo MIC-100 Mobile Primary Crushing Plant , which comes to the transport position without the need for manpower, is the leading crushing plant in the sector with the highest transportation speed.