Turbomix-60 | TEKNİK DETAYLAR | Turbomix-60 | TEKNİK DETAYLAR |
---|---|---|---|
PRODUCTION CAPACITY | 60-80 HOUR | VIBRATING SCREEN SIZE | 1300x4000 mm |
MAXIMUM FEEDING | 380 mm | TOTAL MOTOR POWER | 223kW |
PRIMARY JAW CRUSHER | 600x400 mm | GENERATOR - OPTIONAL | 350 kvA |
JAW/TERTIARY CRUSHER | CLK-60/TK-65 |
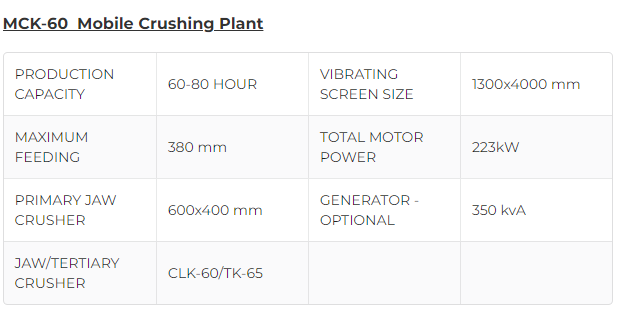
Vibrating Feeder Bunker
FABO Vibrating Feeder Bunkers have been developed by our engineers in a user-oriented manner so that the crusher on which it is positioned can operate with high efficiency.
A1 quality springs, which provide the vibration of the bunker, have been specially designed and their working capacity has been maximized.
Our product, which has a 10 m3 rock feeding feature, is one of the special work machines that our company put forward with its quality and experience. Our product, which is durable and ideal for long-term use, is produced in accordance with CE standards and does not contain any substances that may endanger human health.
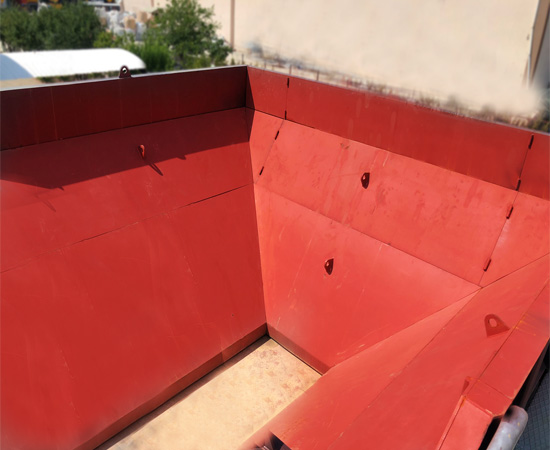
Jaw Crusher
Jaw Crushers are the starting point of production at the MCK-60 Mobile Hard Stone Crushing and Screening Plant. The material poured from the bunker gets crushed into the jaw crusher. Thanks to the hydraulically adjustable jaw opening, the size of the desired product can be changed. It has a robust structure and it serves the user for a long time.
Stones like basalt, granite and other abrasive materials with high silica content can be crushed easily with the jaw crusher and the Tertiary crusher and it has a direct impact on the capacity of the MCK-60 Mobile Hard Stone Crushing and Screening Plant.
It is possible to adjust the FABO jaw crushers with the hydraulic adjustment mechanism. This system allows the lower jaw opening to be adjusted easily and quickly according to the product you want to take from the machine.
Tertiary Impact Crusher
Fabo Tertiary crushers are among our high rotor speed crushers located on the MCK-60 Mobile Hard Stone Crushing and Screening Plant. Its body, which can be opened thanks to 2 hydraulic pistons, provides convenience for maintenance and spare part replacement.
The product crushed in the jaw crusher is discharged to the tertiary crusher with conveyor belts. The products falling into the Tertiary Crusher crush the material by hitting the upper bars of the crusher with the rotor arms rotating at high speed. This process continues until 0-5 mm of product is obtained. When the crushing process is finished, the material is sent to the vibrating screen.
The main factor in product crushing is the rotor and crushing hammers. Fabo engineers did not ignore this important factor and carried out important studies for rotor robustness. Fabo enabled the rotor to work in both directions only for the reason to minimize the wear on the hammers. Rotor rotation speed, opening of crushing hammers can be controlled by the automation system. The rotor, which is described as the heart of the Tertiary Crusher, reaches a speed of 750-1100 rpm. With its high speed capacity, it shreds the loaded product as soon as possible.
Fabo Tertiary Crushers, which is the leader in the production of 0-5 mm products, is the solution partner of its users in production with 100% customer satisfaction.
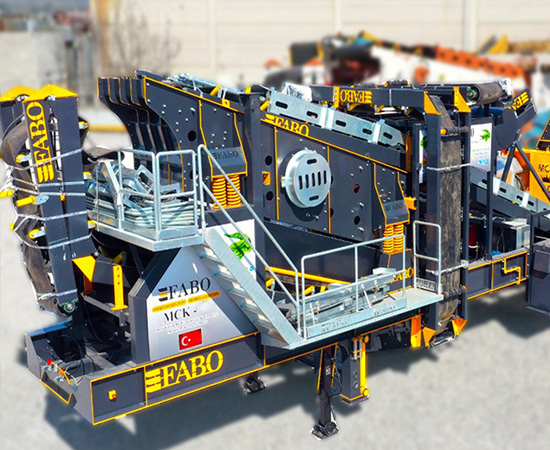
Vibrating Screen
Fabo vibrating screen separate the products coming out of the crusher by means of 4 mesh wires of different sizes. When the desired dimensions are obtained, they are sent to the conveyor belts.
Thanks to the 2 bearings on it, FABO Screens keep the load distribution at the optimum level and offer a long service life. Thanks to 8 specially produced steel springs, it works in the most efficient way and provides maximum capacity.
FABO Screens are a combination of quality, reliability and performance; It provides a long service life even under the toughest conditions. Its unique location on the MCK-60 Mobile Hard Stone Crushing and Screening Plant allows it to work more efficiently. Fabo vibrating screen, which move in harmony with the impact crusher on which it is located, ensure that products in desired sizes are obtained in line with the demands.
Flap System (Optional)
It is a special system that allows the crushed material to be taken with the help of the front stock band, after the necessary adjustments are made with the hydraulic adjustment pendulums of the Primary Impact Crusher in order to receive material from the direct crusher.
According to the desired product dimensions, pendulums can be adjusted to receive products such as 0-31 / 0-63 / 0-150 mm.
The flap minimizes production time with its unique position just in front of the sieve.
In addition, when it is desired to obtain a uniform product with the flap system, it disables the vibrating screen and prevents the screen from wearing out.

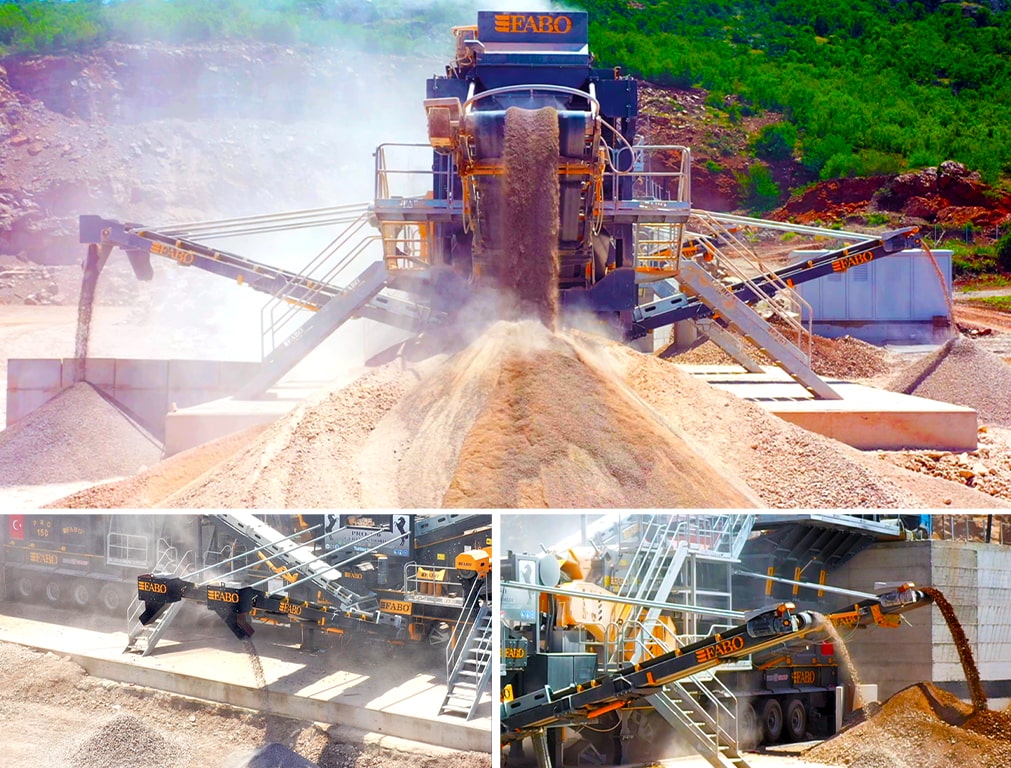
Stock and Return Bands
Fabo folding type feeding, feedback, stock conveyor belts are the vehicles that send the right product to the crusher and the stock area according to the product’s recipe after separeting through the vibrating screen.
With its foldable structure, it minimizes the dimensions of the machine it is on. Optionally, the number and length of tapes can be increased upon the request of the user.
10 mm EP 125 4-ply Band elastics, moving on 4mm st 37 Twisted Sheet, perfectly transport the aggregate coming out of the sieve to the area desired by the user in the most efficient way. The band tires, which are produced resistant to wear, will never let you down and offer a long service life.
Automatic Lubrication System (Optional)
The Automatic Lubrication System is the system in charge of sending the grease that is reduced during the use of the crushing and screening plant and needs maintenance to the relevant part.
It distributes the grease evenly to all components of the mobile crusher that needs lubrication and provides perfect lubrication.
The automatic lubrication system, which provides great ease of maintenance, finishes the lubrication process in seconds without the need for manpower. It allows to use the Mobile Crusher Plant in the most efficient way.
It uses the amount of oil in the most ideal way during lubrication and minimizes the maintenance cost of the user.
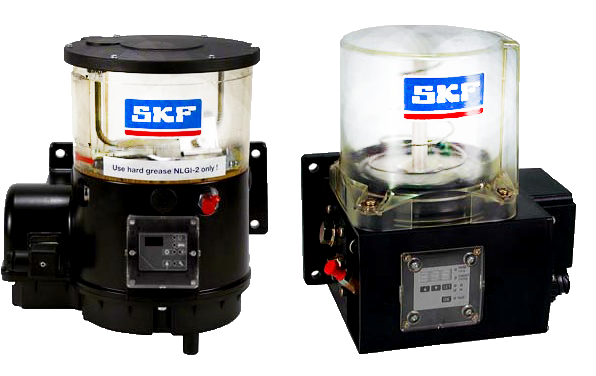
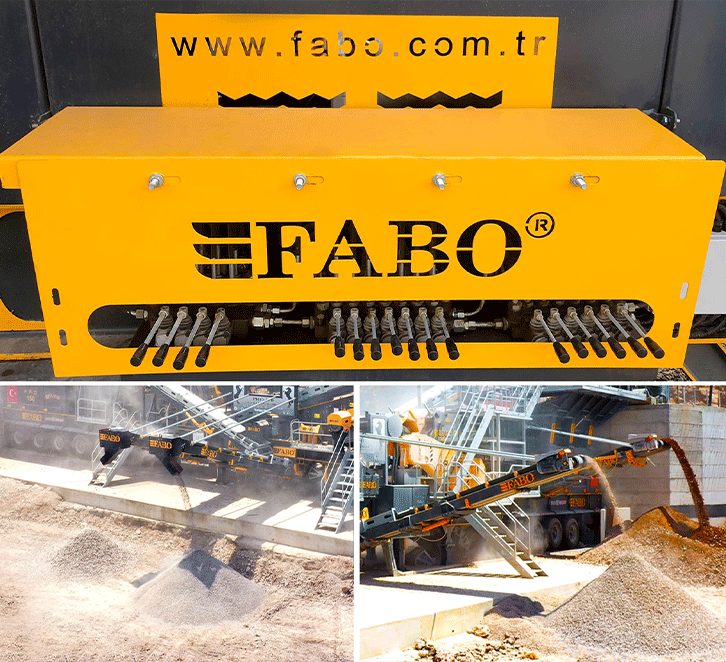
Hydraulic System (Optional)
Hydraulics is the system that enables the parts on the crushing and screening plants to move easily. Opening, closing and moving the machine’s carrying legs, feeding bands, bunker covers and crusher feeder can be given as examples.
Hydraulic System Working Principle:
With the movement of the control arms, the hydraulic oil in can activate and the material to which the hydraulic system is connected the desired direction.
Automation System
MCK-60 Mobile Hard Stone Crushing and Screening Plant is controlled by a full automation system. Thanks to the automation system panel on the machine, the working mode of the machine is adjusted. The working principle of the machine can be easily adjusted according to the shape of the material loaded by the user into the vibrating hopper. Many features such as Crusher Rotor Speed, (Optional) Woobler Feeder Speed, Bunker Vibration Speed, can be adjusted with the automation system.
The automation system, created by Fabo engineers, has been put at the disposal of its users in its most up-to-date form, taking into account all the tests performed from production to delivery.
It offers the opportunity to control the machine from anywhere in the world by using the remote connection feature with internet connection.
The automation system that allows you to use the Mobile Crushing and Screening Plant in the most efficient way has been prepared with PLC and serves its users with the most advanced state of technology.
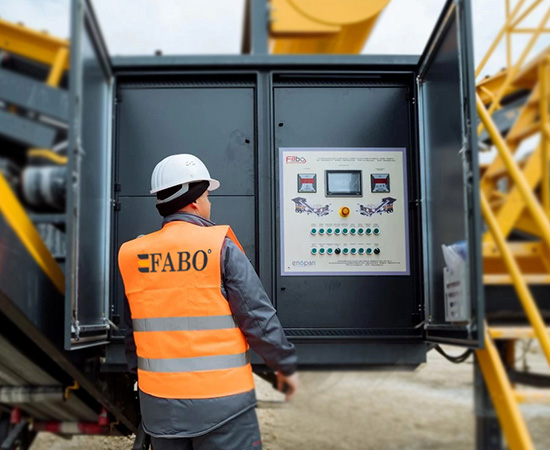
Brake Axle System
The main factor that enables the MCK-60 Mobile Hard Stone Crushing and Screening Plant to be moved easily is the axles at the rear. The load distribution of the crusher is calculated by our engineers and the number of axles and their position are determined.
Shipping
Fabo MCK-60 Mobile Hard Stone Crushing and Screening Plant minimizes the time and cash loss of the user with its ease of transportation. The MCK-60 Mobile Hard Stone Crushing and Screening Plant developed by our engineers can be easily moved on a single chassis with a truck. Fabo MCK-60 Mobile Hard Stone Crushing and Screening Plant, which is moved on axles, is ready for transportation in 10 minutes.
The MCK-60 Mobile Hard Stone Crushing and Screening Plant, which we have created as a result of 18 years of knowledge and work, has been designed in the most ideal way for the user with its crushing and screening capacity and easy transportation.
The brake system in the axle system has increased the life and property safety of the user to the highest level and has written its name in the sector with gold letters with 0% accident rate.
Fabo MCK-60 Mobile Hard Stone Crushing and Screening Plant, which comes to the transport position without the need for manpower, is the leading crushing and screening plant in the sector with the highest transportation speed.
