Turbomix-60 | TEKNİK DETAYLAR | Turbomix-60 | TEKNİK DETAYLAR |
---|---|---|---|
PRODUCTION CAPACITY | 200-300 T/H | IMPACT CRUSHER ROTOR | Ø 1250x1500 mm |
VIBRATING SCREEN SIZE | 2200x5500 mm 1700x4500 mm(Grizzly) | MAXIMUM FEEDING SIZE | 800 mm |
SCREW WASHER SIZE | 800x8000 mm(Twin) | TOTAL MOTOR POWER | 560 kW |
JAW CRUSHER SIZE | 1100x850 mm | GENERATOR – OPTIONA | 700 kvA |
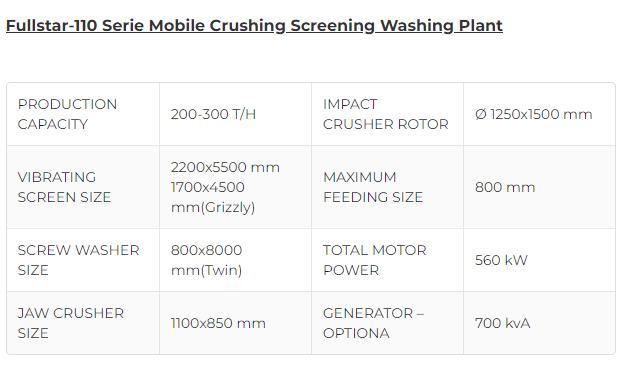
FULLSTAR-110 Mobil Crushing Screening & Washing Plant
FULLSTAR-110 Mobile Crushing and Screening Washing Plant serves our customers with its practical and economical solution for crushing, screening and washing processes.
The crushing and screening washing plant produced on a double chassis provides maximum capacity with this feature. The equipment on it is listed as follows.
- 1,Chassis
Vibrating Feeding Bunker: It transfers the products such as granite, basalt limestone loaded on it to the jaw crusher.
Jaw Crusher: It shreds the material coming from the Feeding Bunker with its strong jaw structure and sends it to the conveyor belt.
Vibrating Washing Screen: The products coming from the Jaw Crusher are discharged to the 2-decked vibrating washing screen. The washing and screening process of the products starts here. A specially designed washing system is installed on each floor. Of the products that are screned in 2 different sizes, those above 0-5mm are transferred to the 2nd chassis. The 0-5 mm sand material is sent to the screw washer.
Conveyor Belt: It transfers the above 0-5 mm size products separated by the vibrating screen to the secondary impact crusher in the 2nd chassis. Also it sends the 0-5 mm size sand products from the screw washer to the stock area.
Spiral Washer: It washes the sand coming from the vibrating screen with 2 helix shafts and dewaters it and then sends it to the stock area.
- 2. Chassis:
Secondary Impact Crusher: The products crushed in the Jaw Crusher are transferred to the Secondary Impact Crusher. The rotor hammers rotating in the crusher crush the products by hitting the impact aprons. The products that come to the desired size are sent to the 2nd vibrating screen with conveyor belts.
Vibrating Screen: The products coming from the Secondary Impact Crusher are discharged to the 4-decked vibrating screen. The screened products in 4 different sizes are sent to the stocking area with stock conveyor belts.
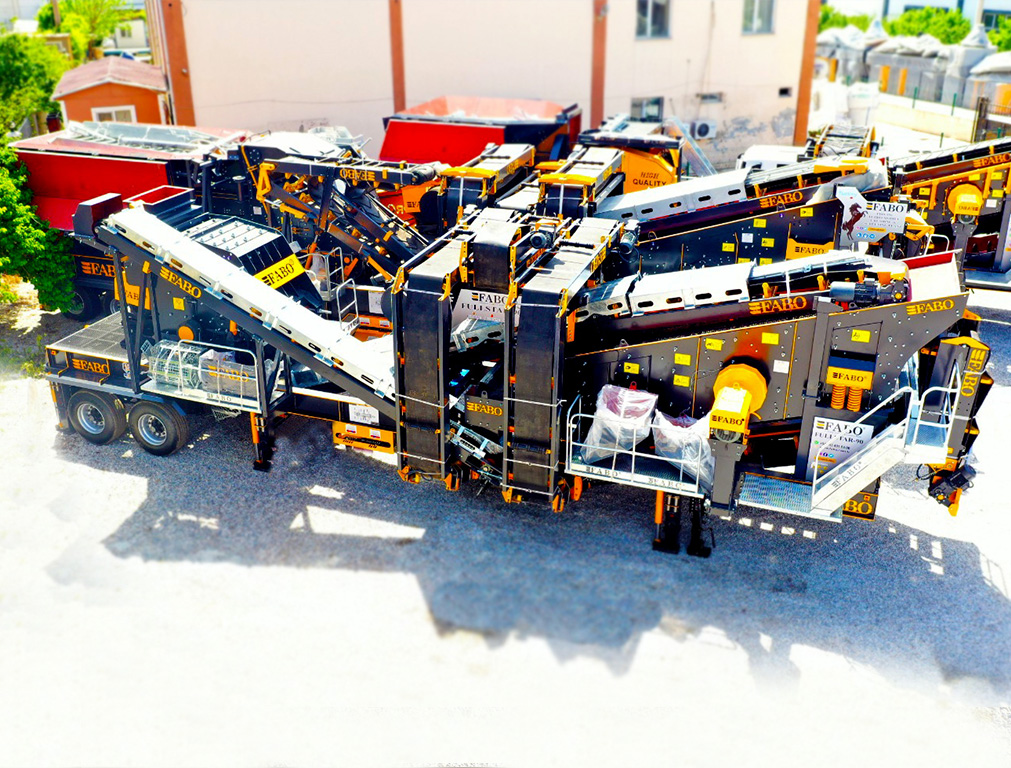
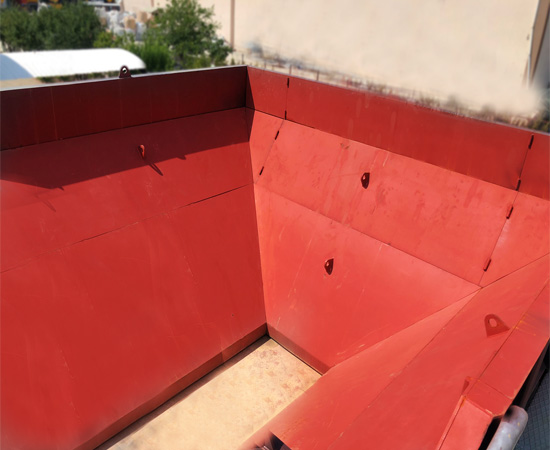
Vibrating Feeder Bunker
FABO Vibrating Feeder Bunkers have been developed by our engineers in a user-oriented manner so that the crusher on which it is positioned can operate with high efficiency.
A1 quality springs, which provide the vibration of the bunker, have been specially designed and their working capacity has been maximized.
Our product, which has a 30 m3 rock feeding feature, is one of the special work machines that our company put forward with its quality and experience. Our product, which is durable and ideal for long-term use, is produced in accordance with CE standards and does not contain any substances that may endanger human health.
Jaw Crusher
Jaw Crushers are the starting point of production at the FULLSTAR-110 Mobile Crushing Screening Washing Plant. The material poured from the bunker gets crushed into the jaw crusher. Thanks to the hydraulically adjustable jaw opening, the size of the desired product can be changed. It has a robust structure and it serves the user for a long time.
Stones like basalt, granite and other abrasive materials with high silica content can be crushed easily with the jaw crusher and the Tertiary crusher and it has a direct impact on the capacity of the FULLSTAR-110 Mobile Crushing Screening Washing Plant.
It is possible to adjust the FABO jaw crushers with the hydraulic adjustment mechanism. This system allows the lower jaw opening to be adjusted easily and quickly according to the product you want to take from the machine.
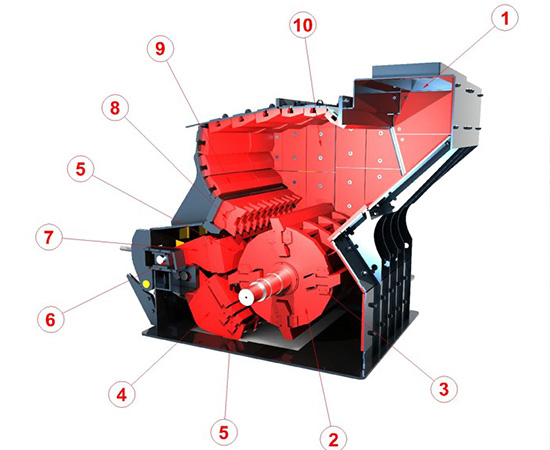
Inner view of the Secondary Impact Crusher
Turbomix-60 |
---|
1-Crusher Feeding Chute |
2-Crusher Rotor |
3- Pallet Holder Lock |
4- Bottom Breaker Adjustment Pandule |
5- Pallet Clamping Bolt |
6- Crusher Middle Pandule Adjustment Slıde |
7-Crusher Middle Pendul |
8- Crusher Middle, Upper Pandulate Castings |
9- Breaker Top Wall Pandules |
10-Breaker Side Linings |
Secondary Impact Crusher
Secondary Impact Crusher used after Jaw Crusher in FULLSTAR-110 Mobile Crushing Screening Washing Plant is the last stop of the crushing process. Here, the broken products are sent to the vibrating screen.
It breaks the products by hitting the pendulum with the rotor arms. It continues until the size specified in the automation system is achieved.
The secondary impact crusher, which is reinforced with high alloy chromium and bolted linings to prevent corrosion, serves its users for many years.
Maintenance:
Ease of maintenance and adjustment is one of the most important advantages of this type of breakers. The hydraulic body opening system, external adjustment of the crusher plates, easy pallet and lining replacement enable this type of crusher to be used easily in construction site conditions.
General Features and Advantages:
-High capacity
-High reduction ratio
-High rate of cubic and fine material production
-Ease of maintenance thanks to the hydraulic adjustment system
-Wear resistant lining plates
-The parts exposed to wear are protected by hardfacing welding
– Pallets and crusher plates are high Chromium and Manganese steel casting
Vibrating Screen
Fabo vibrating screen separate the products coming out of the crusher by means of 4 mesh wires of different sizes. When the desired dimensions are obtained, they are sent to the conveyor belts.
Thanks to the 2 bearings on it, FABO Screens keep the load distribution at the optimum level and offer a long service life. Thanks to 8 specially produced steel springs, it works in the most efficient way and provides maximum capacity.
FABO Screens are a combination of quality, reliability and performance; It provides a long service life even under the toughest conditions. Its unique location on the FULLSTAR-110 Mobile Crushing Screening Washing Plant allows it to work more efficiently. Fabo vibrating screen, which move in harmony with the impact crusher on which it is located, ensure that products in desired sizes are obtained in line with the demands.
Screw Sand Washer (Spiral Sand Washer)
Screw Washer is the section where the sand that is received from the crushing screening and washing process is carried from our FULLSTAR-110 Model, is washed and dewatered and sent to the stock area with the help of the conveyor belts.
The 0-5 mm sand received through the vibrating screen is transferred to the screw washer. The products coming to the washing spiral begin to be washed by the rotation of 2 helix shafts moving in opposite directions. 2 units of helical shafts with 2×7,5 kW motor power provide optimum washing capacity.
Developed by Fabo Engineers as a user-oriented screw washer, after finishing the washing process of the products, it also performs the dewatering process of the product, thanks to the inclination of water flowing in the opposite direction. This feature ensures that the washed sand is stored dry and separated from each other. And it eliminates the need for the user to install an extra dewatering system
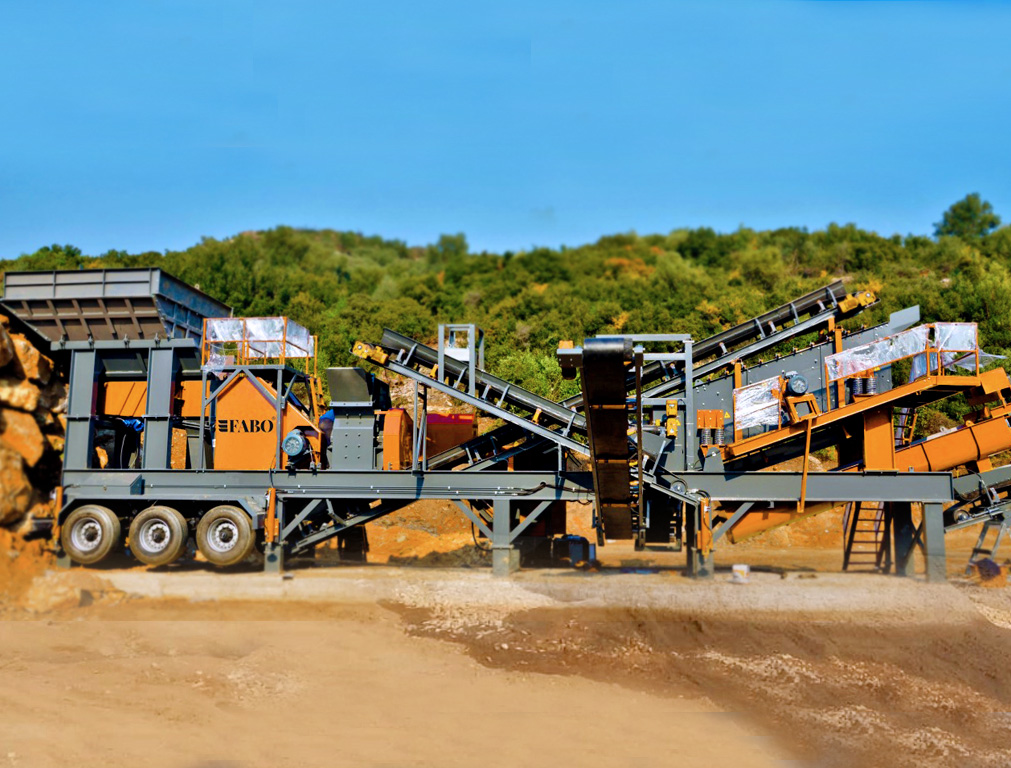
Stock and Return Bands
Fabo folding type feeding, feedback, stock conveyor belts are the vehicles that send the right product to the crusher and the stock area according to the product’s recipe after separeting through the vibrating screen.
With its foldable structure, it minimizes the dimensions of the machine it is on. Optionally, the number and length of tapes can be increased upon the request of the user.
10 mm EP 125 4-ply Band elastics, moving on 4mm st 37 Twisted Sheet, perfectly transport the aggregate coming out of the sieve to the area desired by the user in the most efficient way. The band tires, which are produced resistant to wear, will never let you down and offer a long service life.
Automatic Lubrication System (Optional)
The Automatic Lubrication System is the system in charge of sending the grease that is reduced during the use of the crushing and screening plant and needs maintenance to the relevant part.
It distributes the grease evenly to all components of the mobile crusher that needs lubrication and provides perfect lubrication.
The automatic lubrication system, which provides great ease of maintenance, finishes the lubrication process in seconds without the need for manpower. It allows to use the Mobile Crusher Plant in the most efficient way.
It uses the amount of oil in the most ideal way during lubrication and minimizes the maintenance cost of the user.
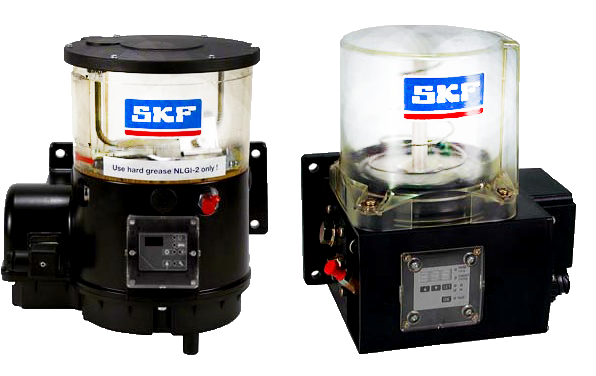
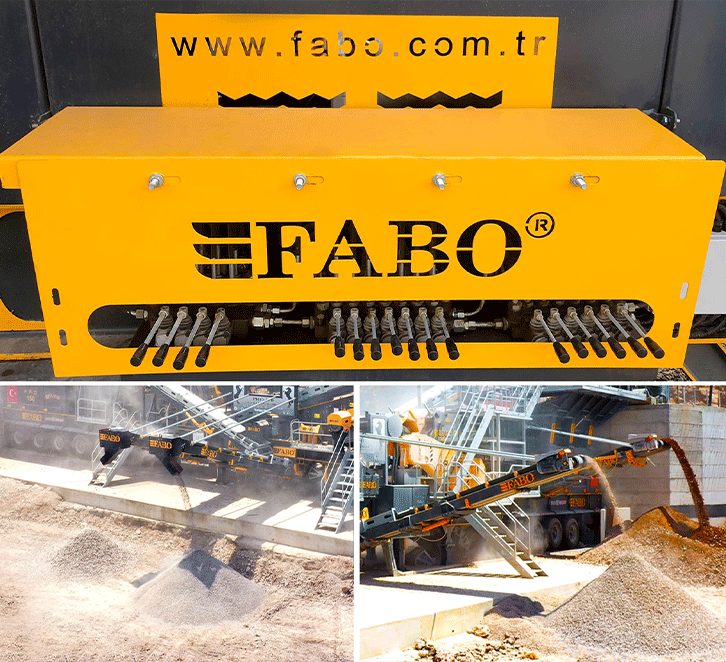
Hydraulic System (Optional)
Hydraulics is the system that enables the parts on the crushing and screening plants to move easily. Opening, closing and moving the machine’s carrying legs, feeding bands, bunker covers and crusher feeder can be given as examples.
Hydraulic System Working Principle:
With the movement of the control arms, the hydraulic oil in can activate and the material to which the hydraulic system is connected the desired direction.
With the automatic lubrication system, it automatically fills the places that need lubrication instead of the user, which minimizes the maintenance cost of the user. It is the product of the meticulous work of our hydraulic system engineers, which completely eliminates the need for manpower.
Automation System
Fullstar-110 Mobile Crushing Screening Washing Plant is controlled by a full automation system. Thanks to the automation system panel on the machine, the working mode of the machine is adjusted. The working principle of the machine can be easily adjusted according to the shape of the material loaded by the user into the vibrating hopper. Many features such as Crusher Rotor Speed, (Optional), Bunker Vibration Speed, can be adjusted with the automation system.
The automation system, created by Fabo engineers, has been put at the disposal of its users in its most up-to-date form, taking into account all the tests performed from production to delivery.
It offers the opportunity to control the machine from anywhere in the world by using the remote connection feature with internet connection.
The automation system that allows you to use the Mobile Crushing and Screening Plant in the most efficient way has been prepared with PLC and serves its users with the most advanced state of technology.
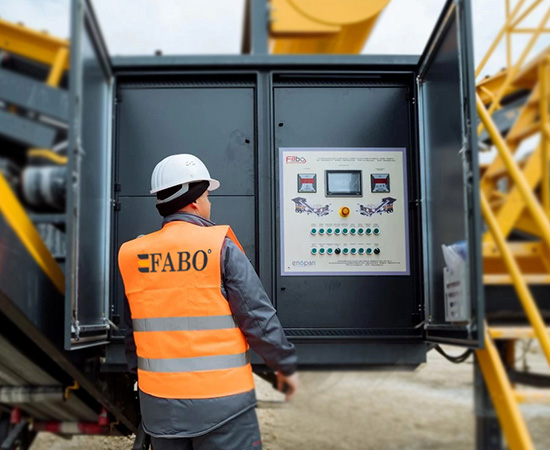
Brake Axle System
The main factor that enables the Fullstar-110 Mobile Crushing Screening Washing Plant to be moved easily is the axles at the rear. The load distribution of the crusher is calculated by our engineers and the number of axles and their position are determined.
Shipping
Fabo Fullstar-110 Mobile Crushing Screening Washing Plant minimizes the time and cash loss of the user with its ease of transportation. The Fullstar-110 Mobile Crushing Screening Washing Plant developed by our engineers can be easily moved on two chassis with two trucks. Fullstar-110 Mobile Crushing Screening Washing Plant, which is moved on axles, is ready for transportation in 10 minutes.
The Fullstar-110 Mobile Crushing Screening Washing Plant, which we have created as a result of 18 years of knowledge and work, has been designed in the most ideal way for the user with its crushing and screening capacity and easy transportation.
The brake system in the axle system has increased the life and property safety of the user to the highest level and has written its name in the sector with gold letters with 0% accident rate.
Fabo Fullstar-110 Mobile Crushing Screening Washing Plant, which comes to the transport position without the need for manpower, is the leading crushing and screening plant in the sector with the highest transportation speed.
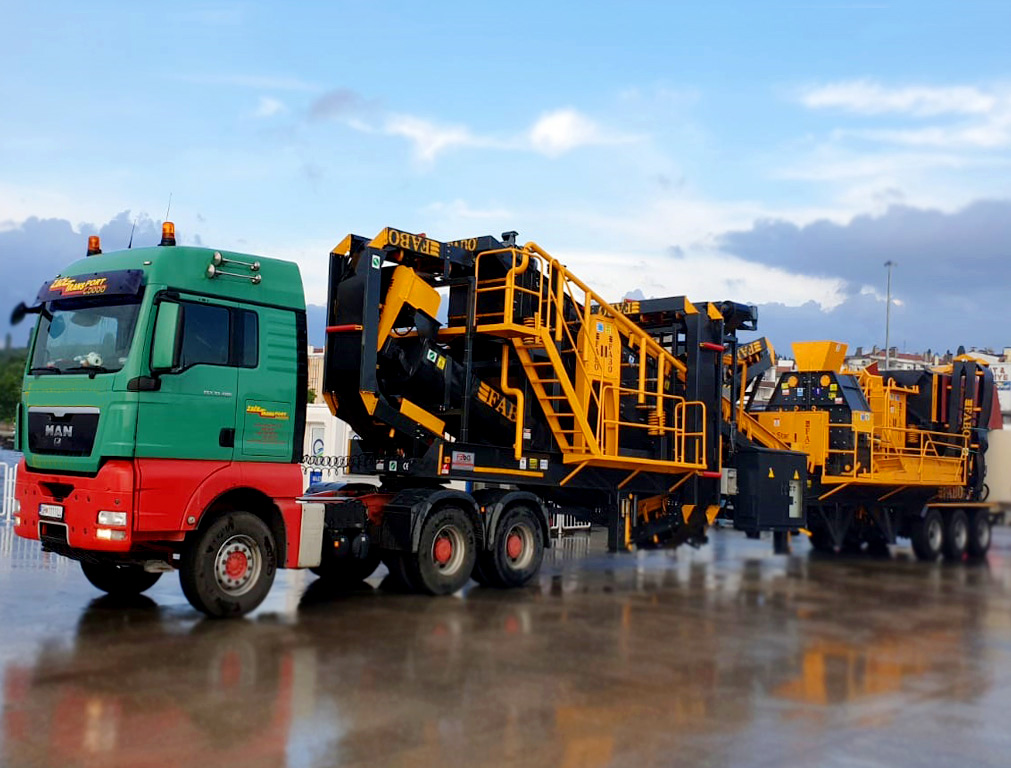